What Are the Raw Materials of Plastic Pneumatic Fittings? (Benefits, Downsides, ...)
When it comes to plastic pneumatic fittings, there are a few important raw materials that must be used.
In this blog post, we will discuss what those materials are and how they are used in the production process. We will also take a look at the benefits and potential downsides of using plastic pneumatic fittings.
Table of Contents
All Parts of Plastic Pneumatic Fittings
Plastic Pneumatic Fittings which are typically used to extend or terminate pipe lengths are also called push-in fittings, push-to-connect fittings, or pneumatic tubing fittings.
Generally speaking, plastic pneumatic fittings can be divided into 2 types: Tube-to-tube pneumatic fitting and Threaded-to-tube pneumatic fitting.
Tube-to-tube pneumatic fittings
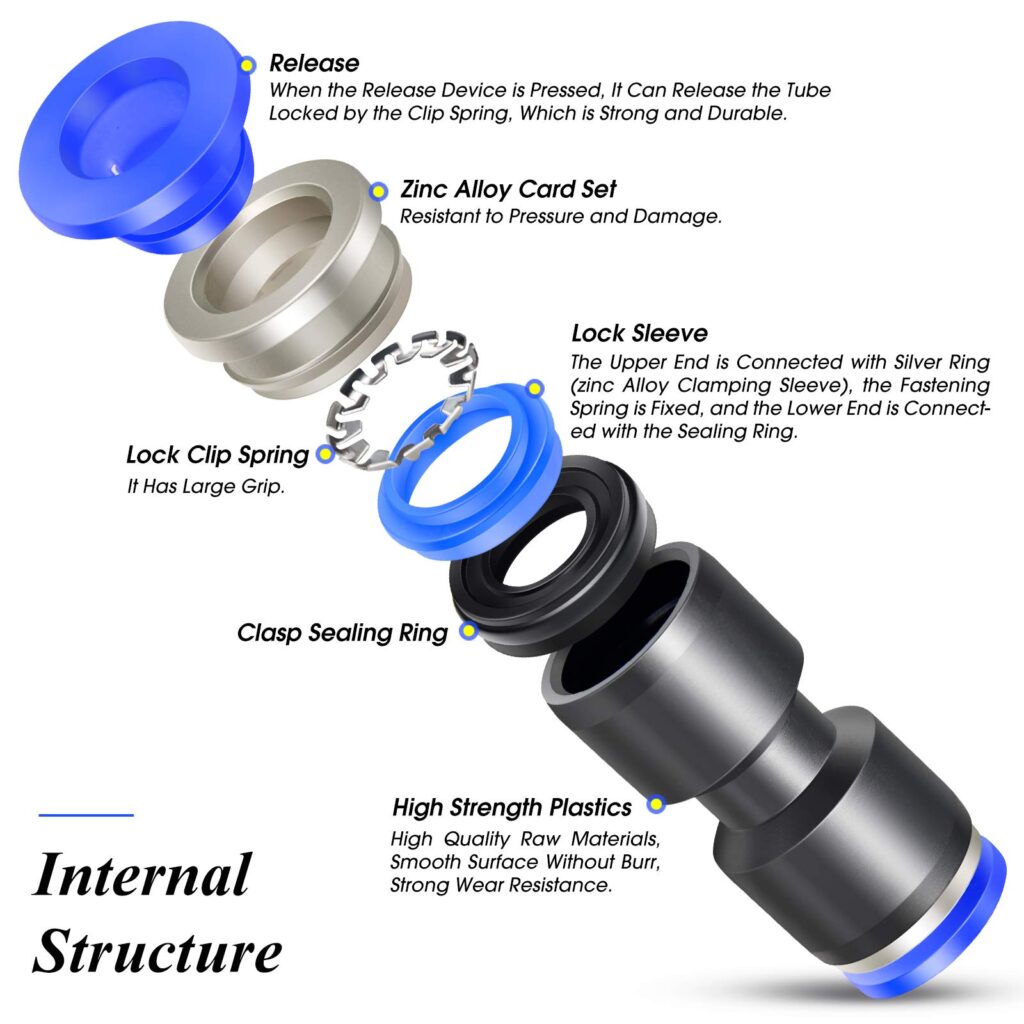
The tube-to-tube plastic pneumatic fittings(connect pipes of the same or reducer size of both sides) usually consist of the following parts:
• Socket body
It is the main component of tube-to-tube plastic pneumatic fittings. It consists of a tight-fitting socket that creates a strong seal when connected to the socket’s counterpart. The socket’s outer surface is usually made from polyamide or polypropylene, which are both highly durable plastics with excellent wear resistance.
• Metal collet
It is the main component of tube-to-tube plastic pneumatic fittings. It consists of a tight-fitting socket that creates a strong seal when connected to the socket’s counterpart. The socket’s outer surface is usually made from polyamide or polypropylene, which are both highly durable plastics with excellent wear resistance.
• O-ring
It is a rubber gasket that helps form an airtight seal between two pipe ends.
• Tube end
The tube end is typically made from brass, aluminum, or stainless steel and serves as the contact point for the metal collet.
• Connector nut
It is a rubber gasket that helps form an airtight seal between two pipe ends.
• Clamp sleeve
The clamp sleeve is a metal ring that helps secure the connector nut and socket body to the pipe.
These tube-to-tube fittings typically disconnect via some type of collar retraction. These connections are convenient for sections of the system requiring frequent disconnection and reconnection.
Threaded-to-tube pneumatic fittings

The threaded-to-tube plastic fittings(one side for tube connections, and the other side for threaded connectors). The raw materials used in plastic pneumatic fittings usually include the following components:
• Sleeve Button(Release):
Polyoxymethylene (POM), is a semi-crystalline thermoplastic that has superior wear resistance, low friction, and good chemical stability(chemical resistance)
• Screwed body:
ABS (Acrylonitrile Butadiene Styrene), PBT (Polybutylene Terephthalate), Polypropylene, Nylon, or other types of materials.
• Body:
Brass, nickel-plated brass, stainless steel
• O-rings:
nitrile rubber, silicone rubber, fluoro rubber, and others.
• Sealing washers:
graphite or other materials.
• Threaded tube end of the fitting
ABS (Acrylonitrile Butadiene Styrene), PBT (Polybutylene Terephthalate), Polypropylene, Nylon, or other types of materials.
• Clamp Spring:
stainless steel
• Thread availability:
Male pipe, Female pipe Body material: Brass; Copper, Aluminum, TFE, PEA, PFA, Thermoplastic.

Threaded Fittings as the name indicates, the threaded fittings have screw threads on their inner (female) or outer (male) surfaces intended to accept connections with mating threads. Threads that provide a simple connection but no assured seal are known as straight threads. A Threaded fitting is a component that can be combined with another to create the right connection (in terms of diameter, thread type, etc.).
Moreover, plastic pneumatic fittings come in different shapes and sizes to meet various applications. The most common categories are straight, elbow, tee, cross, Y-shape, and so on.
Besides the construction designed for plastic pneumatic components, they also feature a wide range of working pressure levels depending on their materials. Plastic pneumatic components usually operate under vacuum and low pressure, however, their working pressure could be up to 20 bar.
Plastic pneumatic components are widely used in many fields, especially for areas that require safety and corrosion resistance. Typical application includes hydraulics, pneumatics, fuel delivery systems, the oil & gas industry, and medical equipment.
The raw materials of plastic pneumatic fittings
Materials Fitting material is important for determining various physical properties of the part.
The main raw materials used to make plastic pneumatic fittings are Polyoxymethylene (POM), polypropylene (PP), polyvinyl chloride (PVC), and nylon.
The sleeve of a plastic pneumatic fitting is usually made of Polyoxymethylene (POM), which is a semi-crystalline thermoplastic that has superior wear resistance, low friction, and good chemical stability(chemical resistance). It is also highly durable, impact resistant, and lightweight. POM can be used for both injection molding and extrusion processing, which makes it ideal for plastic pneumatic fittings.
The body of the pneumatic fitting is usually composed of Polyoxymethylene (POM), polypropylene (PP), or polyvinyl chloride (PVC).
Polypropylene is a thermoplastic type of material, meaning it can be melted down and re-shaped when heated. It has perfect chemical resistance, good flexibility, and broad material compatibility, making it a great choice for use in plastic pneumatic fittings.
Polyvinyl chloride is another type of thermoplastic material that has excellent resistance to chemicals and UV radiation. It exhibits excellent cold flow, bi-axial strength, and yield elongation properties and can be used in exposed applications. It also has good electrical insulation properties, making it ideal for applications where electricity needs to be contained.
Nylon is a synthetic polymer that provides superior strength, flexibility, and durability. It is often used to make plastic pneumatic fittings with a unique shape or size that cannot be achieved using polypropylene or polyvinyl chloride. These materials provide strength and flexibility to the finished product.
Additionally, these raw materials may be combined with additives such as lubricants or fillers in order to increase their performance characteristics.
Furthermore, the presence of plasticizers and UV stabilizers may also be required in order to extend the life of the fitting. It is important that these raw materials are carefully selected in order to ensure that they are compatible with the requirements of the application.
How is the plastic made into a fitting shape and size for use in pneumatic systems?
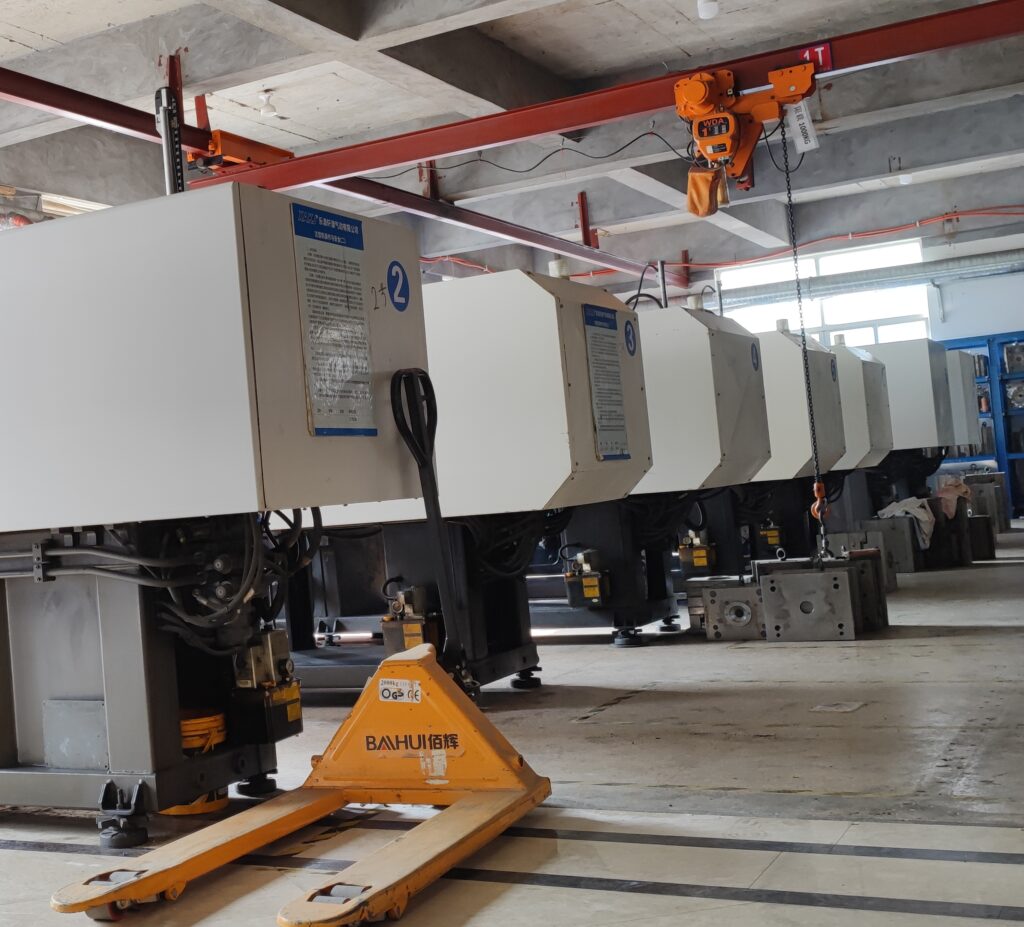
The plastic used in pneumatic systems must first be heated until it becomes more pliable.
The plastic is then molded into the desired shape and size using injection machines and molds designed specifically for this purpose. After the plastic has cooled and hardened, it is cut to its precise measurements with cutting tools such as saws, routers, or laser cutters. The plastic can also be machined to its precise measurements with CNC equipment, which can shape the plastic into any desired shape.
Lastly, the components may require additional finishing operations such as sanding or polishing, depending on the specific application and design requirements. Once all of these steps have been completed, the finished product is ready to be used in a pneumatic system.
What are the benefits of using plastic pneumatic fittings?
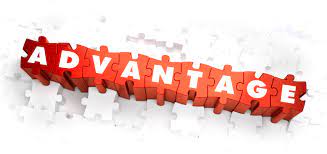
1. Lightweight & easy to Install
Plastic pneumatic fittings are lightweight and fittings installed easily, making them ideal for use in applications that require frequent removal or installation.
Push-in Fittings connect pneumatic pipes(flexible tubing and hose) in a snap, and require no tools or additional hardware.
2. Chemical Resistance
Furthermore, plastic offers good chemical resistance and is unaffected by most chemicals and liquids, making it suitable for use in a wide range of environments.
Plastic Pneumatic Fittings which are typically used to extend or terminate pipe lengths are also called push-in fittings, push-to-connect fittings, or pneumatic tubing fittings.
Generally speaking, plastic pneumatic fittings can be divided into 2 types: Tube-to-tube pneumatic fitting and Threaded-to-tube pneumatic fitting.
Plastic Pneumatic Fittings which are typically used to extend or terminate pipe lengths are also called push-in fittings, push-to-connect fittings, or pneumatic tubing fittings.
Generally speaking, plastic pneumatic fittings can be divided into 2 types: Tube-to-tube pneumatic fitting and Threaded-to-tube pneumatic fitting.
Plastic Pneumatic Fittings which are typically used to extend or terminate pipe lengths are also called push-in fittings, push-to-connect fittings, or pneumatic tubing fittings.
Generally speaking, plastic pneumatic fittings can be divided into 2 types: Tube-to-tube pneumatic fitting and Threaded-to-tube pneumatic fitting.
3. Wide Applications
Plastic pneumatic parts are also extremely durable, allowing them to endure even the most demanding Pneumatic applications.
4. Versatile
Plastic fittings are available in a variety of shapes and sizes, allowing fluid flow to be combined or split apart and thus making them a versatile option that can be used in many different applications.
5. Cost-effective
Finally, plastic pneumatic fittings are relatively cost-effective compared to other types of fittings, making them a great choice for budget-minded projects.
In conclusion, plastic pneumatic fittings are a great choice for many applications due to their lightweight, chemical durability, wide application range, versatility, and cost-effectiveness. They provide an easy-to-use solution that can meet the needs of all Pneumatic logic control systems.
Are there any potential downsides in using plastic pneumatic fittings?
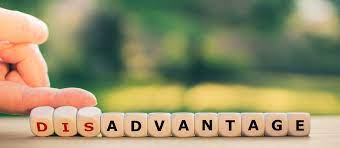
Yes, there are some potential downsides to using plastic pneumatic push-in fittings in industrial or commercial settings.
Plastic is generally not as corrosion-resistant as metal fittings and may be more susceptible to damage from wear and tear over time.
Additionally, depending on the type of plastic used, the strength and durability of the fittings can also vary, making them less suitable for high-pressure applications.
Furthermore, plastic is not as temperature resistant as metal fittings and may crack or deform if exposed to extreme temperatures.
Finally, plastic pneumatic fittings must be inspected regularly to ensure that they are still in working order and free of any cracks or other damages that could lead to leaks.
Taking the time to properly inspect and maintain plastic fittings can help to reduce the potential downsides and ensure the reliable operation of your system.
However, it is important to carefully consider the potential downsides of using plastic fittings in order to determine whether or not they are the best option for your specific application.
When properly maintained and inspected, plastic pneumatic push-in fittings can provide a reliable and cost-effective solution for many types of installations.
If you have any questions about the different types of plastic pneumatic fittings available or their potential advantages and disadvantages, please don't hesitate to contact us.
What should you consider when choosing between different types of fittings?
When choosing between different types of fittings, it is important to consider the following factors:
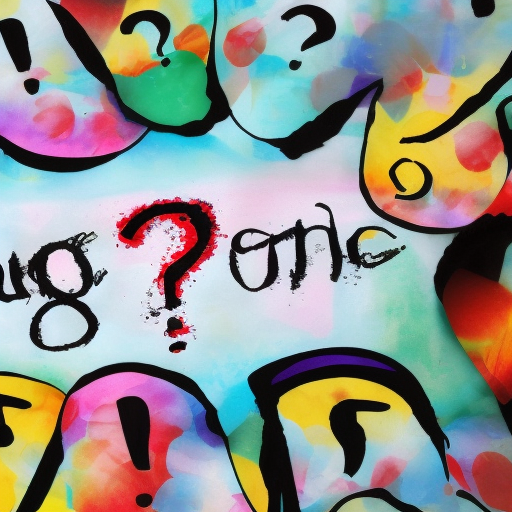
1. Materials
The type of material that the fitting will be connecting. Different materials require different types of fittings and connectors.
2. Proper Sizing & Shape
The size and shape of the parts being connected. Different fittings are designed for different sizes and shapes to connect various flexible vessels(hoses), so make sure you choose the right fitting for your application.
3. Higher Pressure Connection
The operating pressure range is the working range of pressures or the pressure ratings at which the fitting was designed to operate, typically measured in pounds per square inch (psi). Operating above or below this rating could cause the fitting to fail (i.e. break, leak, lose its seal). Different fittings have different ratings and it is important to choose a fitting that can handle the pressure requirements of your application. Operation pneumatic fittings must have a higher pressure rating than the system they are connecting.
4. High-Temperature Durability
The operating temperature range is the working range of temperatures or the temperature ratings at which the fitting was designed to operate, measured in degrees Fahrenheit (°F) or degrees Celsius (°C). Operating above or below this rating could cause the fitting to fail. The temperature range that the fitting will need to operate in. Some materials are suitable for high temperatures while others may require special fittings for low temperatures.
5. Seal Tape(Coating)
The type of fluid or gas that is being connected. This will determine what kind of sealing is needed to ensure a safe and secure connection. Plated fittings have a plating, surface treatment, or coating which provides enhanced thermal characteristics, chemical resistance, excellent corrosion resistance, or other desirable surface characteristics. Tight seal tapes can also be used to ensure no leaks from the fitting.
6. Cost
Cost considerations should also be taken into account when selecting the right fitting for your application. Different fittings can vary in price, so it’s important to find the most cost-effective solution for your needs.
7. Environment
Finally, the environment in which the fitting will be used should be taken into account. Different fittings are designed for different environments and it’s important to choose a fitting that can handle any environmental conditions that may arise.
Conclusion
When selecting the right fitting for your needs, it is important to consider the type of material being connected, the size and shape of the parts, the pressure rating, temperature range, fluid or gas type, cost considerations, and the environment.
By taking all of these factors into account you can make sure that you are choosing a fitting that will provide a safe and secure connection for your application.